Spektr Group has been accredited by ECITB for the third...
Read moreBolting Services
Bolted Joint Integrity – Copy
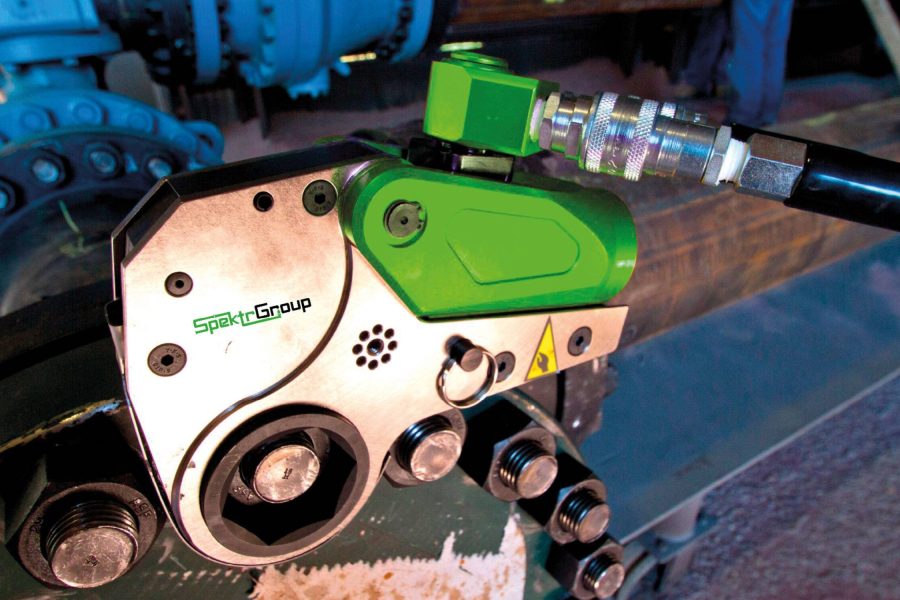
Overall, the collaboration between Spektr Group and Kinetics Controls & Innovation Ltd. holds great promise for advancing the oil and gas industry in Azerbaijan, fostering economic development, and contributing to the country’s energy security and sustainability objectives.
Their diverse range of services includes:
1. Wellhead Seal Isolations
Two-part, time-activated, various viscosity sealant which self-energises under differential pressure when cured. Bridges and isolates large gaps and holes in seal structures, unlike pressure-activated sealants which require small gaps and high pressures to activate. Rigless isolations successfully deployed worldwide reinstating barriers to maintain safe and effective production.
2. Gate Valve Isolations
One-part, non-curing, high viscous sealant product which is deployed into the valve cavity filling scores, scratches and damaged areas around the gate and seat area creating an isolation. Very effective alternative to plastic packing and ideal for re-energising damaged “P” seals.
- Isolate gate valves to allow intervention rig up.
- Provides a repeatable isolation for failed valve stem packing leaks.
- Remains in the valve cavity much longer than grease.
- Protects against well debris and corrosive fluids.
- Operational temperature of -50° to +250°C.
- Displace and replace valve grease providing a superior high-temperature lubricant.
- No Issues with future valve operating torque, production flow, wireline or coiled tubing activity
3. Packer and Casing Shoe Isolations
Time-activated sealant. Cures to soft flexible gel material. High compression value but a low torsion/tear threshold. Designed and ormulated to provide isolations within annuli preventing well fluid migration. The sealant is weighted to sink through existing annuli fluids. Small volumes required, no squeezing or bull heading required.
4. Control Line Leak Repair
One-part, non-curing gel sealant product designed to isolate hydraulic control line leaks in downhole safety valve (DHSV) control line compression fittings where the hydraulic fluid is leaking out of the system while under pressure.
- Maintains the functionality of a downhole safety valve (DHSV).
- A genuine alternative to pressureactivated sealants.
- Neutrally buoyant and will remain in a suspended position.
- Successfully pressure tested up to 10,000psi.
- Operational temperature -50°C to +175°C.
- Expected lifespan of 25 years if left undisturbed.
5. Control Line Plugging
Two-part, time-activated sealant which self-energises under differential pressure when cured. Control line plugging is used to reduce rig time and increase safety when pulling completions for workover or abandonment.
- The sealant is used on control lines, creating plugs to completely block and isolate the line.
- This application can be deployed at the same time as ongoing deep set plugging operations – “Sim Ops”.
- Cures to a solid yet flexible material.
- Successfully pressure tested up to 10,000psi.
- Operational temperature -50°C to +250°C.
- Expected lifespan of 25 years if left undisturbed.
6. Pipeline and Process Valve Isolations
Failed isolations can be detrimental to your operation, causing you delays and downtime. There is no need to have a lack of barriers delay your inspection, repair and maintenance programme. Reduce your delays and get production back online with our fully engineered pipeline and process valve isolations. At KCI we understand the pressure operators are under to maintain assets and reinstate valuable production.
As it becomes increasingly more difficult to obtain isolations on ageing valves, KCI’s fully engineered pipeline and process valve isolations will help to minimise downtime and reinstate valuable production safely and effectively.
Ring Gasket Groove Repair
Mac-Seal 06 offers a quick, safe, robust, and cost-effective solution. Time-activated and available in various viscosities depending on your requirements.
- Sealant is quick to prepare and can be installed by the team on site with minimum downtime.
- Mix and apply Mac-Seal 06 to the upward-facing flange.
- Install the gasket and press to displace the sealant.
- Remove excess and reposition inside the gasket.
- Apply Mac-Seal to the downward-facing flange.
- Mate the two flanges together and tighten.
- The upper and lower flange sealant meet, bond and cure to create a single isolation.
- Pressure testing can take place after the sealant has cured.
Our Works
The Benefits of Flange Management in Industrial Projects
Effective flange management goes beyond being a simple technical requirement—it...
Read moreFlange Management Scope Successfully Completed
We are pleased to announce the successful completion of the...
Read more